Whether it’s a skyscraper under construction, a bridge undergoing maintenance, or a historical monument being restored, one thing remains constant: the vital role of scaffolding. But not just any scaffolding – we’re talking about system scaffolding, the engineered backbone that provides safe and efficient access for workers at height. This article delves into the characteristics of system scaffolding, exploring its key attributes, diverse types, and the compelling advantages it offers.
Key Attributes of System Scaffolding
System scaffolding distinguishes itself from traditional scaffolding through its meticulous design and engineered precision. Let’s break down the key attributes that set it apart:
Modular Design
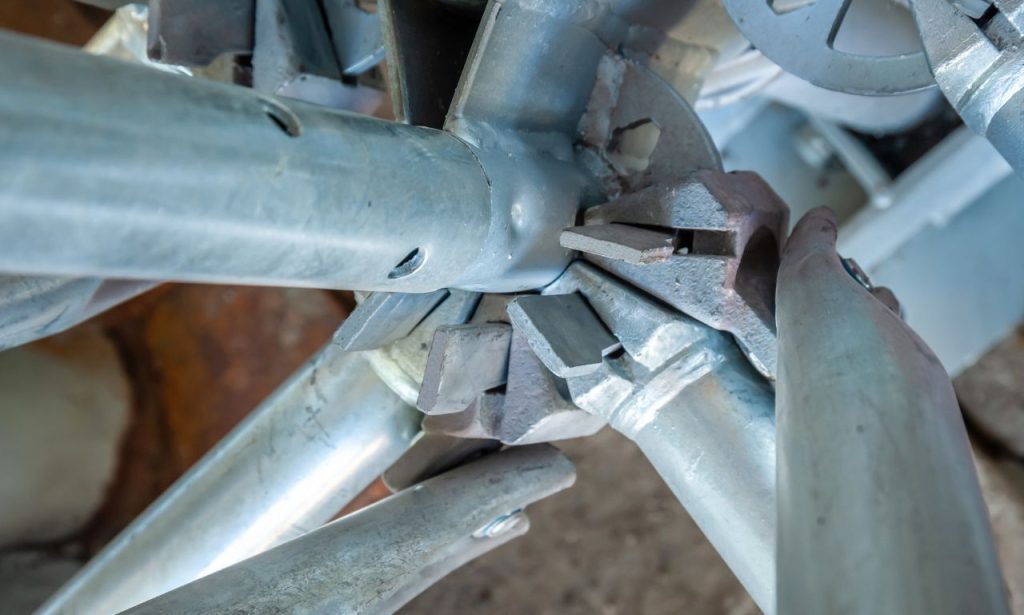
Imagine building with LEGOs – that’s the essence of modular design in system scaffolding. Instead of cumbersome timber planks and loose fittings, system scaffolding utilizes prefabricated, standardized components that connect seamlessly. These components, including:
- Standards (Vertical Members): The upright supports that bear the primary load.
- Ledgers (Horizontal Members): Connect standards horizontally to create a framework.
- Braces (Diagonal Members): Provide lateral stability and rigidity.
- Base Plates: Distribute the load from standards onto the ground.
- Platforms: Provide a safe working surface for workers.
Safety Standards Compliance
When it comes to working at height, safety isn’t just a priority – it’s paramount. System scaffolding is engineered with stringent safety standards in mind, adhering to regulations set by organizations like OSHA (Occupational Safety and Health Administration) and ANSI (American National Standards Institute). Here’s how system scaffolding prioritizes worker safety:
- High-Strength Materials: Components are typically constructed from high-grade steel or aluminum, ensuring structural integrity and the ability to withstand heavy loads.
- Secure Locking Mechanisms: Unlike traditional scaffolding with its reliance on ropes and wedges, system scaffolding employs robust locking mechanisms that prevent accidental disengagement or slippage.
- Integrated Safety Features: Many systems incorporate features like guardrails, toe boards, and access ladders, providing passive fall protection and minimizing the risk of accidents.
- Regular Inspections and Maintenance: System scaffolding is designed for easy inspection, allowing for regular checks to identify and address any potential issues before they escalate.
Load Capacity
System scaffolding isn’t just about reaching heights; it’s about doing so while supporting significant weight – workers, tools, materials, and even light machinery. The load capacity of system scaffolding is determined by factors like:
- Component Material and Dimensions: Thicker steel components with larger cross-sections can handle heavier loads.
- Scaffold Configuration: The arrangement and spacing of standards, ledgers, and braces influence the overall load distribution and capacity.
- Grounding Conditions: Stable and level ground is crucial to ensure the scaffolding’s ability to bear the intended load safely.
Before erecting any system scaffolding, it’s essential to consult engineering drawings and manufacturer specifications to determine the maximum permissible load for the specific configuration. Overloading the scaffolding can have catastrophic consequences, compromising its structural integrity and jeopardizing worker safety.
Stability and Durability
Construction sites are dynamic environments, often exposed to harsh weather conditions, varying temperatures, and potential impacts. System scaffolding is built to withstand these challenges, ensuring stability and durability over the long haul.
- Corrosion Resistance: Components are often galvanized or coated with protective finishes to prevent rust and corrosion, extending their lifespan and maintaining structural integrity.
- Weather Resistance: System scaffolding is designed to withstand exposure to rain, wind, and UV radiation without compromising its performance or safety.
- Impact Resistance: The robust construction of system scaffolding provides a degree of impact resistance, safeguarding against accidental collisions or dropped objects.
Types of System Scaffolding
Now that we’ve delved into the characteristics of system scaffolding, let’s explore the different types commonly used in the industry:
Ringlock System Scaffolding: The Versatile All-Rounder
Ringlock scaffolding has gained immense popularity for its versatility, ease of use, and robust design. Its defining feature is the “ring” disc located at the connection points of the standards. Ledgers and braces are secured to these rings using wedge-shaped locking pins, creating a highly stable and secure structure.
Key Features of Ringlock Scaffolding:
- Multi-Directional Connections: The ring disc allows for connections at various angles (typically 8 different positions), providing exceptional flexibility in design and configuration.
- Fast and Efficient Assembly: The wedge-lock system enables quick and secure connections, reducing assembly time and labor costs.
- High Load Capacity: Ringlock scaffolding is known for its impressive load-bearing capabilities, making it suitable for heavy-duty applications.
- Wide Range of Applications: From building construction and bridge maintenance to industrial projects and event staging, Ringlock scaffolding’s versatility makes it a popular choice across industries.
Cuplock System Scaffolding
Cuplock scaffolding is another widely used system known for its simplicity, strength, and ease of erection. It features a “cup” welded at fixed intervals along the standards. Ledgers are inserted into these cups and secured with a locking pin, creating a rigid and secure connection.
Key Features of Cuplock Scaffolding:
- Simple and Intuitive Design: The cup and pin connection system is straightforward to use, requiring minimal training for assembly.
- High Strength and Stability: The fixed cup positions and robust locking pins create a highly stable and secure scaffolding structure.
- Cost-Effective Solution: Cuplock scaffolding is often a more budget-friendly option compared to other systems, making it attractive for projects with cost constraints.
- Suitable for Various Applications: While commonly used in general construction and maintenance projects, Cuplock scaffolding is also suitable for lighter-duty industrial and event applications.
Kwikstage System Scaffolding
As its name suggests, Kwikstage scaffolding is designed for rapid assembly and dismantling, making it ideal for projects where time is of the essence. It features a unique “v-shaped” ledger that connects to the standards using a simple hammer-in locking mechanism.
Key Features of Kwikstage Scaffolding:
- Rapid Assembly and Dismantling: The hammer-in locking system allows for incredibly fast erection and dismantling, significantly reducing labor costs and project timelines.
- Lightweight yet Strong: Kwikstage scaffolding components are relatively lightweight, making them easier to handle and transport while still providing sufficient strength for most applications.
- Ideal for Repetitive Configurations: The system’s speed and ease of use make it particularly well-suited for projects with repetitive scaffolding configurations, such as multi-story buildings with consistent floor plans.
- Cost-Effective for Large Projects: The time savings and reduced labor requirements associated with Kwikstage scaffolding can lead to significant cost savings, especially on large-scale projects.
Advantages of System Scaffolding
The characteristics of system scaffolding we’ve explored culminate in a range of advantages that make it the preferred choice for modern construction and maintenance projects:
Cost-Effectiveness
While the initial investment in system scaffolding might seem higher than traditional timber scaffolding, the long-term cost savings are undeniable.
- Reduced Labor Costs: Faster assembly and disassembly translate into lower labor expenses, as fewer man-hours are required for erection and dismantling.
- Increased Material Lifespan: Durable components with corrosion-resistant finishes extend the lifespan of the scaffolding, reducing the need for frequent replacements.
- Minimized Downtime: The system’s stability and weather resistance minimize the risk of weather-related delays or damage, keeping projects on schedule.
Improved Workflow Efficiency
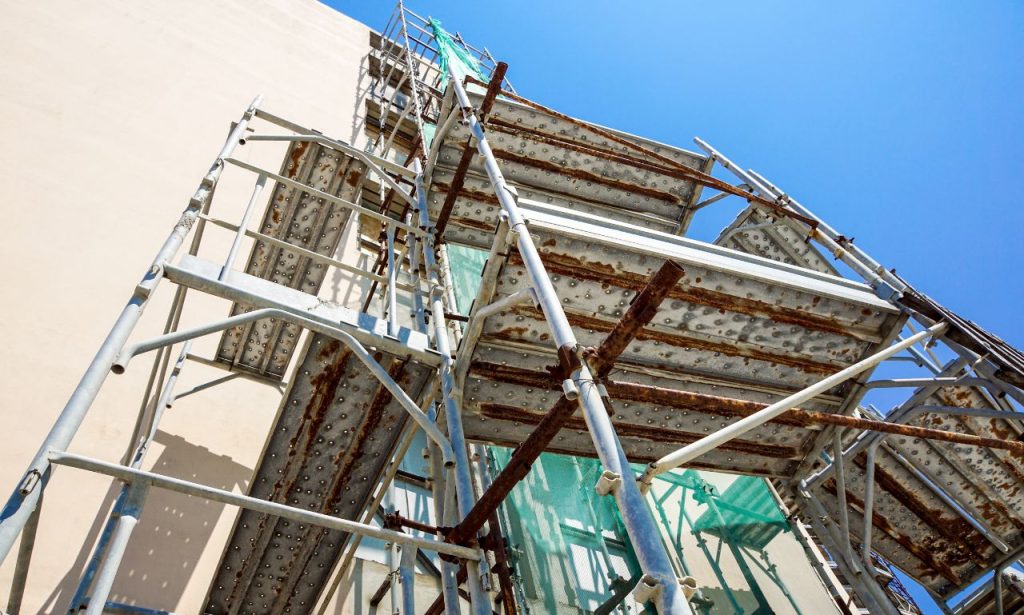
System scaffolding doesn’t just get the job done; it gets it done efficiently, optimizing workflows and maximizing productivity on site.
- Faster Erection and Dismantling: Modular components and intuitive connections streamline the assembly process, allowing workers to quickly erect and dismantle the scaffolding as needed.
- Flexible Configuration Options: System scaffolding can be easily adapted to accommodate various project requirements, ensuring optimal access and support for different tasks.
- Enhanced Worker Mobility: Platforms, stair towers, and other access features facilitate safe and efficient movement of workers and materials at height.
Enhanced Worker Safety
Safety is paramount in any work environment, and system scaffolding’s commitment to worker well-being is unwavering.
- Stringent Safety Standards Compliance: System scaffolding is designed and manufactured to meet or exceed industry safety regulations, ensuring structural integrity and minimizing risks.
- Secure Locking Mechanisms: Robust locking systems prevent accidental disengagement or slippage of components, providing a stable and secure working platform.
- Integrated Safety Features: Guardrails, toe boards, access ladders, and other integrated features provide passive fall protection and enhance worker safety.
Conclusion
System scaffolding represents a paradigm shift in how we approach working at height. Its characteristics – modular design, safety compliance, load capacity, stability, accessibility, ease of use, versatility, and customization options – converge to create a system that elevates both efficiency and safety on construction and maintenance projects. By understanding the characteristics of system scaffolding and choosing the right system for your specific needs, you can ensure a secure, efficient, and successful project from the ground up.
ALSO READ: The Most Commonly Used Pilot Devices
FAQs
A: With proper maintenance and care, system scaffolding can last for many years, even decades. Regular inspections, timely repairs, and proper storage contribute to its longevity.
A: Yes, system scaffolding can be adapted for use on uneven ground using adjustable base plates or screw jacks to ensure a level and stable base. However, it’s crucial to consult with a qualified engineer to determine the appropriate adjustments and ensure structural integrity.
A: Workers involved in the erection, dismantling, or alteration of system scaffolding must be trained by a competent person to recognize and minimize hazards associated with scaffolding. Training should cover topics like hazard identification, fall protection, safe assembly procedures, and load limitations.